Document ressource - Rugosité des surfaces usinées
2. Généralités sur la rugosité des surfaces usinées
2.3. Phénomènes pouvant perturbés la coupe et l'état de surface engendré
Les hypothèses de base des modélisations précédentes peuvent être mises à défaut lorsque les paramètres de coupe sont mal définis.
Trajectoire non parfaite de l'outil par rapport à la pièce :
La forme de la surface réellement engendrée par l'outil peut être affectée par les perturbations de la trajectoire de outil par rapport à la pièce, occasionnées par des vibrations importantes de l'un de ces éléments (ou des deux). Lorsque les conditions dynamiques (flexibilité et inertie des éléments, insuffisance d'amortissement mécanique) sont telles que les variations oscillatoires de cette trajectoire deviennent auto-entretenues, il en résulte des perturbations périodiques de la surface découpée. Elles prennent la forme de marques ou de stries plus ou moins accusées, qui peuvent modifier sensiblement la rugosité du profil idéal défini par la trajectoire théorique de l'outil. C'est le phénomène de broutement.
Les manifestations de ces phénomènes dépendent de nombreux facteurs, tels que :
- les éléments cinématiques du mouvement outil/pièce (vitesse de rotation, avance) ;
- les flexibilités dynamiques du système machine-outil-pièce ;
- les jeux des organes de la machine et ses imperfections mécaniques (dentures d'engrenages,
usure des glissières, etc.) ;
- l'orientation de l'effort de coupe résultant.
Leur étude systématique et la prédétermination des conditions de broutement sont
extrêmement délicates et sortent du cadre de ce travail. Il est néanmoins essentiel de connaître
l’existence de ce phénomène et ses incidences éventuelles sur la qualité de l'usinage.
En tournage, le choix d'un grand rayon de bec, favorable pour réduire la rugosité théorique,
peut accroître les risques de broutement si l'outil ou la pièce sont assez flexibles. Dans ce cas,
l'angle de direction moyen de la partie active de l'arête coupante peut être sensiblement plus
faible que l'angle de direction conventionnel, défini par la partie rectiligne de cette arête. La
composante radiale de l'effort de coupe s'en trouve alors augmentée, ce qui accentue la flexion
de la pièce et les risques de vibration. Il peut donc être nécessaire de faire un compromis pour le choix d'un rayon de bec de valeur optimale, en tenant compte de la rigidité du système
pièce-outil-machine.
Forme de la partie active de l'outil non parfaite.
Le second facteur déterminant la rugosité de la surface usinée découle des imperfections inhérentes à l'action de l'outil tranchant.
L’état du bec de l'outil c'est-à-dire de son arête et des défauts d'état de surface de ses faces, l'hétérogénéité du matériau, ainsi que les imperfections de la coupe donnent une rugosité de la surface usinée différente de la rugosité théorique. Ils donnent lieu à des défauts d'ordre 4. Cette différence est plus ou moins sensible suivent les conditions opératoires (nature des matériaux, vitesse de coupe et avance, type d'outil et son usure, etc.). Les cas les plus défavorables, à cet égard, sont ceux où l'on usine des métaux ductiles (acier doux par exemple) à faible vitesse et très faible avance. En effet, ces conditions entraînent généralement la formation, au voisinage de l'arête tranchante, d'une "arête rapportée" (ou "copeau adhérent", Fig.2.3.4) dont les fragments sont appliqués sur la surface usinée par la pression de l'outil. Il en résulte un mauvais état de surface.
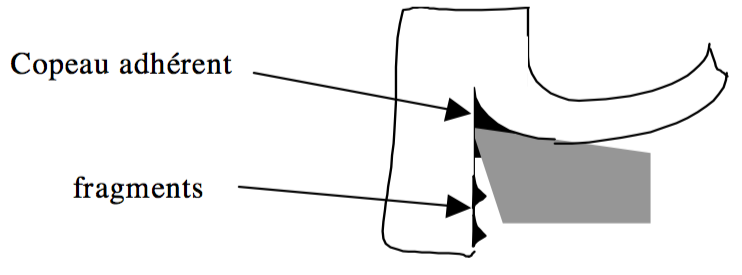
Fig.2.3.4 : Arrête rapportée
Il faut noter que l'effet défavorable des faibles avances sur la rugosité s'avère contradictoire avec leur influence directe sur la rugosité théorique. Ici encore, ceci conduit à un compromis pour le choix d'une valeur optimale de l'avance pour l'obtention d'un bon état de surface. Par contre, le choix d'une vitesse de coupe élevée (dans la limite de l'endurance à l'usure de l'outil), est un élément généralement favorable à cet égard.